The oil and gas industry is making a dramatic shift toward automating processes, controls, and systems. From drilling operations to saltwater disposal (SWD) facilities, the industry is looking to improve operational efficiencies and get hands off equipment.
The problem with having so many operators shifting to this new way of doing business is the lack of standardization. There doesn’t seem to be a real understanding of what automation and remote monitoring are and what they aren’t.
The information that is readily available focuses primarily on the aspects of where the technology originated, and not enough about the implications those changes mean to the oilfield.
To be honest, automation is only a single piece of a much larger puzzle. Connectivity, reliability, calibrated alarms and remote monitoring are all important aspects of integrated systems that make up the new oilfield.
Remote Monitoring: Going Beyond Automation
Even a fully integrated automation system that uses cutting-edge IPC hardware and software still has the potential for incidents. Spills and larger incidents are not only costly but also dangerous for field personnel. When an incident occurs, reaction time is measured in seconds, not hours.
With the majority of upstream and midstream facilities operating without personnel on site, the ability to remotely monitor operations (even if they’re automated) is vital to keep facilities incident-free and preventing downtime.
What Is Remote Monitoring?
At the most basic level, a simple analog display of tank levels could classify as remote monitoring. But other than displaying a snapshot in time, this degree of “remote monitoring” does little to improve the safety and efficiency of oilfield operations.
When thinking of remote monitoring, the entirety of your system should be considered and represented in the data/information being evaluated:
- Tanks and pits should have level indicators.
- Pipelines should be monitored with flow meters and pressure gauges.
- Potential points of failure should be equipped with alarms that have been calibrated for your specific operations.
- Cameras should provide visual verification of the integrity of the system.
All of this requires reliable connectivity to provide real-time information that can support staff and field technicians.
This begs the question — How capable is your support staff?
Remote Monitoring means more than “Observe and Report”
The human aspect of remote monitoring is vital to the prevention and mitigation of incidents at your facilities. The people assigned to monitor your operations must understand the operations and be able to identify potential failures before they pose a risk to the facility.
Monitoring without technical knowledge of the operation or without the ability to act is a remote monitoring solution equivalent to “observe and report.” This level of remote monitoring gives oilfield operators a false sense of security when operations are running smoothly, but does next to nothing should an incident occur.
In essence, the ability to act, is what makes a remote monitoring service valuable to the operator.
Points To Consider
When evaluating remote monitoring solutions, does the service provider have technicians, electricians, and other subject matter experts on call twenty-four hours a day assigned specifically to your operations?
What is the response time of remote intervention? More importantly, what is the response time of field technicians?
While automation is getting the most attention, the support structure that allows automated systems to function is an important component of a fully integrated system. Remote monitoring and field technicians that respond to incidents close the gap that allow the reduction of incidents and maximized uptime.
SitePro is an automation software solution provider that can fully integrate your system with customized technical components (hardware and software) while experienced technicians and electricians can respond to your facilities in the event of an incident, often before it happens.
To learn more about our software and how it can help you remotely manage your facilities, click the button below.
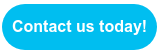