The rise of digital technology has made it easier for oilfield operators to address data management issues. As the demand for oil and gas increases- and thus the need for more efficient processing- it is becoming clear that inefficiencies persist throughout the upstream and midstream sectors.
One major problem we face as an industry is how vendors, service companies, and operators continue to use proprietary systems with different data formats and definitions. This lack of standardization creates challenges when transferring, converting, and processing information. To compound the issue, a large part of the oil and gas industry also still runs on paper. While paper trails come with several benefits, they cannot keep up with the volume of information and demand throughout the industry.
An example of this outdated approach is especially prevalent among saltwater disposal operations- specifically their ticketing systems.
Oilfield companies use tickets to keep track of everyday operations and product transfers. They play a crucial role in the supply chain because they document transactions and help vendors and other companies stay on track of delivered products and services.
Relying solely on a paper-based ticketing process, however, often causes operators, administrators, and auditors to encounter issues like missing, inaccurate, or illegible information. Furthermore, it can create headaches when compiling and organizing data for regulatory reporting.
The Drawbacks of Paper-Based Field Tickets
Invoice Disputes and Decreased Days Sales Outstanding
Paper-based field tickets lead to a higher number of days sales outstanding (DSO). DSO — or the average number of days required to collects payments after invoicing — helps operators ensure a streamlined and efficient job-to-invoice process. Manual systems and paperwork result in a high DSO because of slow and unnecessary clerical processes involved in paperwork. The manual handling of documents is time-consuming and error-ridden.
Often, companies with high DSO use slow, outdated, paper-based field ticketing systems. The oil and gas industry is more susceptible to higher DSO because of its tedious documentation processes, complex cost cycles, and regulatory requirements that must be met before a field ticket can be approved and finalized.
Other factors like illegible handwriting and incorrect bill rates contribute to invoice disputes as well. The manual typing and re-typing of data could result in high administrative costs. Manual data reports also prevent the spread of accurate, real-time information, making it difficult for managers to make accurate decisions about their business.
Service companies and oilfield equipment manufacturers face a similar burden because they need to manage and budget expenses. Without real-time visibility into supplier spending habits and a repository for critical information, it becomes harder to document data, reduce DSO, and increase cash flow.
Lengthy Processing and High Operational Costs
Field tickets function as a receipt when companies make on-site visits to carry out services such as delivering produced water at a saltwater disposal (SWD) facility. When performing the job, a provider issues a field ticket that describes the service or product volume, which warrants the authorization of a field supervisor at the facility.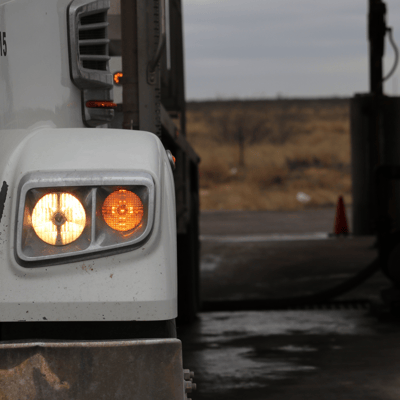
Research shows, however, that a lengthy, handwritten process is prone to errors and fraud. In fact, it could take 22 days or more to process a field ticket into an invoice. The estimated period could extend further, depending on the problems in other parts of the ticketing process.
The extended processing of a paper ticket could also lead to higher operational and labor costs. With upstream and midstream companies processing hundreds or thousands of tickets every month, errors and reconciliation unnecessarily increase operational costs and delay payment.
Different products have different prices associated with their disposal, storage and processing. So accessing data from service providers and generating an invoice quickly leads to more successful resource allocation planning. If you step back and see the waste inherent in paper tickets, it is clear that even the smallest operation would benefit from getting away from them.
Paper-Based Field Ticketing Affects Different Buyers
Processing paper documents fails to add value or produce profits the way other methods can. Paper-based methods reduce the ability of a company to plan for the future since it often results in delayed and inaccurate information.
Additionally, paper tickets are also expensive to route from one person to another. In turn, this affects buyers on different levels, including field operators, accounts payable departments, and upper management.
- Field operators are responsible for verifying and signing off on service work. They ensure that the job or product type and volume match the ticket information and codes for invoicing. Tickets with illegible or inaccurate information could cause delays in the reconciliation process.
- Accounts payable department verifies whether the submitted invoices are accurate. After the review process, they examine the invoices and correct ticket errors. They are also responsible for reconciling inaccurate information prior to filing.
- Operations management makes decisions about how to keep operations running efficiently as well as planning future jobs. The decision-making process could suffer, however, when the information is too thin. Without sufficient, accurate data, planning turns to guesswork.
- Suppliers suffer with slow paper processes because of high DSOs. Service charges that fail to match existing contracts or previously stated agreements typically cause delays. Another setback includes the process of chasing down approvers for the proper coding and sign-off.
In a nutshell, paper-based processes end up using too many resources that oilfield companies that could instead use to take on higher-value work with greater returns for the business. The lag time in document processing and data exchange forces companies to work on past mistakes instead of planning for the future and staying competitive in the market.
The Benefits of Shifting to Digital Ticketing
Fortunately, many SWD companies are evolving with the rest of the oil and gas industry to a more efficient technology-based approach. They are using advancements to increase productivity and reduce costs. Using digital ticketing solutions accelerates the review and invoicing process because it utilizes cloud technology and makes data validation easier.
Digital ticketing solutions move everything online to speed up field ticketing operations. They also allow for real-time oversight. Operation managers have the freedom to create job tickets and send them to crew members in real time.
Digital Field Tickets Reduce Costs and Improve Overall Operations
Digital field tickets are electronic versions of the paper-based field ticket. They contain operational data that suppliers send to operators so they can authorize job completion or product delivery. Service companies require acknowledgment through an electronic signature from authorized personnel following the completion of services or the distribution of materials. This way, digital field tickets ensure the payment between the operators and the service companies.
Adopting digital, e-ticketing solutions provides tremendous opportunities for process improvement and promotes closer cooperation between operators and suppliers. Some of the benefits include:
- Enhancing efficiency in remote locations – Workers often operate in remote areas that do not have a stable internet connection. This could pose a challenge because field crews need to stay connected continuously, even on-site. E-ticketing solutions are available both online and offline, allowing members to perform their tasks, alter tickets, record relevant site data and attach documents or photos. After the field workers return to an area with a reliable Internet connection, they need to synchronize their tablet or PC and make the information available to invoice.
- Streamlining the job-to-invoice process – Operations and accounting staff in the office and in the field can use e-ticketing to produce a more efficient, streamlined and valuable job-to-invoice process. This results in a single, consolidated platform that stores product rates, equipment, materials, price books, job-related documents and more. A single platform makes it easier for operators to reduce mistakes in invoicing and job quotes. This way, they can avoid dispatching duplicate jobs and unavailable equipment.
- Reduced day sales outstanding – The slow, clerical process of paper-based, Excel, and other manual systems results in a high DSO. Moreover, it increases the chances of error and consumes valuable time. Digital tickets makes existing processes more efficient because it speeds up field data collection and customer invoicing. It also ensures that approvers receive accurate field service information. With a more streamlined approach to field operations and accounting, oil and gas companies can reduce DSO and get paid more quickly.
- Quicker and easier invoice approvals – Field approvers often end up spending too much time on administrative tasks like searching for correct codes or reconciling inaccurate information. Automated coding and validation can, however, shorten field ticket approval times to days or hours. Users can, for instance, use e-ticketing platforms to identify exceptions like duplicate tickets and mismatched codes. This makes it possible to automatically approve or dispute invoices based on ticket information.
- Customizable alerts that keep users in the know – Many digital ticketing software feature alert systems that allow users to create their text or email alert notifications. Users can customize these alerts depending on time, user, and purpose. This way, they can filter notifications according to the crew, client, office and business segments and inform them of new developments at a moment’s notice. Using the alert system can improve customer service, slash fuel costs and enhance communication among team members.
- A central intelligence accounts payable department – Digitizing tasks and automating processes help companies boost productivity and streamline tactical functions. The various departments in your company will benefit from having access to accurate information from a single source anytime and anywhere. Oilfield companies can use the central hub of intelligence to achieve better supplier collaboration and understand supply chain relationships better. Dynamic e-ticketing systems will also fully integrate with your existing accounting software, making the use of the new electronic ticketing system completely seamless.
Streamlining Your Ticketing and Regulatory Reporting Processes
SitePro offers a robust digital field operations management solution that allows saltwater disposal companies like yours to control the supply chain in real time. Our digital ticketing solution, Ticket Center, takes the hassle out of paper-based processes for service companies and E&Ps. Digitize tickets, bulk edit information, access regulatory data for haulers and wells, and export that data for invoicing or other reporting purposes.
Easily access that data in our regulatory center, which can automatically fill out your monthly forms for reporting purposes.
You can use our software through local access control at a facility or via our cloud-based app. Our access control version of the software is accessible through a password protected touchscreen that captures haul ticketing information and simplifies the manual data gathering process.
Not interested in incorporating new hardware at your site? No problem. Our Ticket Center and Regulatory Center are available software-only, allowing you to manually upload your paper tickets or connect your other digital ticketing platform to utilize SitePro's features. Yup, we can integrate with any system you're using, no extra hardware required.
Interested in learning more about streamlining your ticketing and reporting system? We would love to chat.
